Our Products
Polyacrylamide / anionic polyacrylamide RHEOMAX 9030 can be replaced by Chinafloc A6508
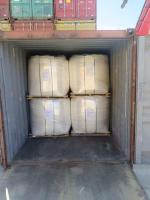
anionic polyacrylamide RHEOMAX 9030 can be replaced by Chinafloc A6508
RHEOMAX 9030 is a kind of anionic polyacrylamide with very high hydrolysis degree and medium molecular wieght ,mainly used for aluminum and other nieral processing.it can be replaced by Chinafloc A6508 with good performance.
Anionic polyacrylamide (APAM) is a versatile polymer widely used in various industrial processes due to its ability to enhance sedimentation, flocculation, and filtration. In the context of aluminum processing and treatment, APAM plays several crucial roles. Here is an in-depth analysis of its applications in aluminum production and treatment:
1. Flocculation and Sedimentation in Bauxite Ore Processing
One of the primary applications of anionic polyacrylamide in the aluminum industry is in the processing of bauxite ore to extract alumina (Al₂O₃), the primary raw material for aluminum production. The Bayer process is the most common method for extracting alumina from bauxite. During this process, bauxite is digested in a solution of sodium hydroxide, resulting in a slurry that contains both dissolved alumina and various impurities, such as silica, iron oxides, and titanium dioxide.
Role of APAM:
Flocculation: Anionic polyacrylamide is added to the slurry to promote the aggregation of fine particles, such as silica and iron oxides, into larger flocs. The negatively charged groups on the APAM molecules interact with positively charged particles in the slurry, leading to the formation of flocs.
Sedimentation: Once the fine particles are aggregated, they become heavier and settle more quickly to the bottom of the settling tanks. This process is crucial for separating the solid impurities from the liquid alumina solution. The use of APAM significantly enhances the efficiency of this separation, resulting in clearer supernatant and higher-quality alumina extraction.
2. Clarification of Alumina Liquor
After the initial sedimentation process, the resulting alumina-rich liquor still contains some suspended solids and fine particles that must be removed before further processing. Anionic polyacrylamide is used to clarify the liquor by facilitating the removal of these residual impurities.
Role of APAM:
Improved Filtration: The addition of APAM to the alumina liquor helps in agglomerating the remaining fine particles, making them easier to filter out. This results in a cleaner alumina solution, which is essential for the subsequent precipitation of alumina crystals.
Reduced Energy Consumption: By improving the filtration process, APAM reduces the energy required for filtration and the frequency of filter maintenance, leading to cost savings in the production process.
3. Wastewater Treatment
The aluminum production process generates significant amounts of wastewater, particularly during the washing and cooling stages. This wastewater often contains suspended solids, heavy metals, and other pollutants that need to be treated before disposal or reuse. Anionic polyacrylamide is widely used in the treatment of aluminum industry wastewater due to its effective flocculating properties.
Role of APAM:
Flocculation of Suspended Solids: APAM is added to the wastewater to aggregate suspended solids, such as alumina particles, metal oxides, and other impurities, into larger flocs. This makes it easier to remove these solids through sedimentation or filtration.
Heavy Metal Removal: APAM can also aid in the removal of heavy metals, such as aluminum, iron, and chromium, from wastewater. The polymer's negatively charged groups can bind with positively charged metal ions, facilitating their precipitation and removal.
Improved Sludge Dewatering: The use of APAM in wastewater treatment also enhances the dewatering of sludge, reducing its volume and making it easier to handle and dispose of.
4. Enhancement of Alumina Refinery Efficiency
In an alumina refinery, the efficiency of various processes, such as precipitation, thickening, and filtration, is critical to the overall productivity and cost-effectiveness of aluminum production. Anionic polyacrylamide plays a significant role in optimizing these processes.
Role of APAM:
Precipitation Control: During the precipitation of alumina from the sodium aluminate solution, APAM can be used to control the size and growth of alumina crystals. This is important because the size and purity of the alumina crystals directly impact the efficiency of the smelting process and the quality of the final aluminum product.
Thickening of Slurries: APAM is used in thickeners to increase the concentration of alumina in the slurry by promoting the aggregation of fine particles. This results in a higher yield of alumina and reduces the load on downstream filtration equipment.
Filtration Enhancement: By improving the filtration characteristics of slurries, APAM reduces the time and energy required for filtration, leading to increased throughput and lower operating costs.
5. Aluminum Hydroxide Production
In the production of aluminum hydroxide (Al(OH)₃), which is an intermediate product in the Bayer process, anionic polyacrylamide is used to improve the efficiency of the precipitation and separation processes.
Role of APAM:
Crystal Growth Modification: APAM can influence the growth of aluminum hydroxide crystals, promoting the formation of larger and more uniform crystals. This is important for achieving the desired physical properties of the final aluminum hydroxide product.
Sedimentation of Aluminum Hydroxide: The use of APAM in the precipitation tanks helps in the rapid settling of aluminum hydroxide crystals, leading to improved separation and recovery rates.
6. Environmental Compliance and Sustainability
The use of anionic polyacrylamide in aluminum production also contributes to environmental compliance and sustainability by reducing the environmental impact of the production process.
Role of APAM:
Reduction of Solid Waste: By enhancing the separation and recovery of alumina and aluminum hydroxide from slurries and waste streams, APAM helps reduce the amount of solid waste generated during production.
Water Recycling: The use of APAM in wastewater treatment allows for the recycling of treated water back into the production process, reducing the overall consumption of fresh water and minimizing the environmental footprint of the refinery.
Minimization of Chemical Usage: The efficiency of APAM in flocculation and sedimentation reduces the need for additional chemicals in the treatment process, leading to a lower environmental impact and cost savings.
7. Application in Downstream Processes
Beyond the primary aluminum production process, anionic polyacrylamide is also used in various downstream processes, such as casting, rolling, and surface treatment of aluminum products.
Role of APAM:
Cooling Water Treatment: In aluminum casting and rolling operations, large amounts of cooling water are used to control the temperature of the metal. APAM is used in the treatment of cooling water to remove suspended solids and prevent the buildup of scale and deposits on equipment.
Surface Treatment: In surface treatment processes, such as anodizing and electroplating, APAM can be used to treat rinse water and effluents, ensuring that they meet environmental discharge standards.
8. Challenges and Considerations in APAM Application
While anionic polyacrylamide offers numerous benefits in aluminum production, there are also challenges and considerations that must be addressed to optimize its use.
Considerations:
Dosage Control: The effectiveness of APAM is highly dependent on the correct dosage. Overdosing or underdosing can lead to suboptimal results, such as incomplete flocculation or excessive chemical usage. Careful monitoring and control of the dosage are essential.
Compatibility with Other Chemicals: APAM may interact with other chemicals used in the production process, such as caustic soda or lime. It is important to ensure that these interactions do not negatively impact the process or the quality of the final product.
Environmental Impact: Although APAM is generally considered safe for use in industrial processes, its environmental impact should be carefully evaluated, especially in terms of biodegradability and toxicity in aquatic environments. The selection of environmentally friendly variants of APAM may be necessary in some cases.
9. Future Trends and Innovations
As the aluminum industry continues to evolve, there are several trends and innovations related to the use of anionic polyacrylamide that are worth noting.
Innovations:
Advanced Polymer Formulations: Ongoing research and development in polymer chemistry are leading to the creation of more advanced APAM formulations with improved performance characteristics, such as faster flocculation, higher efficiency, and lower environmental impact.
Automation and Process Control: The integration of automation and process control technologies in aluminum refineries is enabling more precise control over the application of APAM, resulting in better process optimization and reduced chemical usage.
Sustainability Initiatives: The aluminum industry is increasingly focused on sustainability, and the use of APAM is likely to play a key role in achieving these goals. Innovations in the recycling and reuse of APAM-treated water and sludge are expected to reduce the environmental footprint of aluminum production.
Conclusion
Anionic polyacrylamide is a critical component in the aluminum industry, with applications ranging from ore processing and alumina extraction to wastewater treatment and environmental compliance. Its ability to enhance flocculation, sedimentation, and filtration processes makes it indispensable in achieving efficient and sustainable aluminum production. As the industry continues to evolve, the role of APAM is likely to expand further, driven by advancements in polymer science and a growing emphasis on sustainability.