Our Products
Product Center / Hydroxamated(hydroxamic acid) polyacrylamide used for aluminum factory
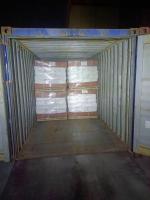
Application of Hydroxamated (Hydroxamic Acid) Polyacrylamide in Aluminum Factory
In aluminum production—particularly within alumina refineries using the Bayer process—hydroxamated polyacrylamide plays a critical role in the clarification and separation of red mud from sodium aluminate liquor. These specialized polymers are high-performance flocculants functionalized with hydroxamic acid groups, giving them enhanced selectivity and binding affinity for metal oxides such as iron and aluminum. Their main application is in the settling and dewatering stages of bauxite residue (red mud) management, where they significantly improve process efficiency and reduce caustic losses.
1. Background: The Bayer Process in Aluminum Plants
The Bayer process is the dominant method used to extract alumina (Al₂O₃) from bauxite ore. The key steps are:
-
Digestion – Bauxite is dissolved in hot, concentrated caustic soda (NaOH), forming a sodium aluminate solution.
-
Clarification – Insoluble impurities (red mud) are separated from the clear aluminate solution.
-
Precipitation – Alumina hydrate is recovered by cooling and seeding the liquor.
-
Calcination – The hydrate is heated to produce alumina.
Among these stages, clarification is one of the most challenging due to the fine particle size and colloidal nature of red mud. Efficient solid-liquid separation is vital for recovering caustic soda and maximizing throughput. This is where hydroxamated polyacrylamide becomes essential.
2. Chemistry of Hydroxamated Polyacrylamide
Hydroxamated polyacrylamide is a modified anionic or nonionic polyacrylamide in which some of the carboxylic groups are converted to hydroxamic acid groups (–CONHOH). These groups form strong chelates with trivalent metal ions such as Fe³⁺ and Al³⁺, commonly found in bauxite residue.
Key characteristics include:
-
High molecular weight for bridging flocculation
-
Hydroxamic functionality for targeted binding to metal oxide surfaces
-
Stability in high-pH conditions typical of Bayer liquors (pH 13–14)
3. Main Application: Red Mud Flocculation and Settling
The primary application of hydroxamated polyacrylamide in aluminum factories is as a flocculant for red mud settling. In the clarification stage, it is dosed into the primary settler or thickener feedwell, where it rapidly adsorbs onto red mud particles and promotes floc formation.
Mechanism:
-
The hydroxamic groups chelate iron and aluminum oxides.
-
The polymer chains bridge multiple particles.
-
Large, dense flocs form and settle rapidly.
-
Clarified liquor rises to the top and is collected for downstream processing.
This process improves separation, reduces suspended solids in the overflow, and results in denser underflow mud that is easier to manage and wash.
4. Benefits in Aluminum Refining
Hydroxamated polyacrylamide delivers numerous operational and economic benefits to alumina refineries:
a. Faster Settling Rates
-
The polymer enables rapid flocculation of fine particles.
-
Higher settling rates increase thickener throughput and allow greater mud loading.
b. Clearer Overflow Liquor
-
The strong metal-binding properties ensure better particle capture.
-
Overflow liquor has reduced turbidity and suspended solids, improving efficiency in subsequent precipitation steps.
c. Higher Underflow Density
-
Larger, more compact flocs lead to denser mud.
-
This reduces the volume of mud to be transported or processed further.
d. Reduced Caustic Loss
-
Red mud often traps caustic soda.
-
Efficient flocculation minimizes soda retention in the residue, reducing chemical costs and environmental risk.
e. Shear-Resistant Flocs
-
Flocs are robust and withstand the turbulence in feedwells and piping systems.
f. Improved Washer Performance
-
When applied in washer circuits, the polymer enhances mud compaction and improves wash water recovery.
5. Points of Application in Aluminum Plants
Hydroxamated polyacrylamide can be used at several stages in the refinery:
-
Primary Clarifier (Settler Feed)
-
Most common application point.
-
Enhances red mud settling and overflow clarity.
-
-
Secondary Thickeners
-
Used to improve density and reduce mud carryover.
-
-
Washer Circuits
-
Enhances compaction and reduces soda loss in counter-current decantation systems.
-
-
Red Mud Disposal Systems
-
Used to dewater mud before stacking or disposal.
-
6. Comparison with Conventional Flocculants
Compared to standard anionic polyacrylamide, hydroxamated variants offer superior performance due to their chemical affinity for metal oxides.
Property | Standard PAM | Hydroxamated PAM |
---|---|---|
Metal oxide binding | Weak to moderate | Strong chelation |
Settling speed | Moderate | Fast |
Overflow clarity | Good | Excellent |
Mud compaction | Good | Improved |
Dosage efficiency | Moderate to high | High at lower dosages |
Performance at high pH | Variable | Stable and reliable |
7. Product Formats and Handling
Hydroxamated polyacrylamide is available as:
-
Water-in-oil emulsions
-
Dry powders
-
Ready-to-use solutions
Typical dosages are in the range of 10–50 ppm, depending on bauxite quality, mud characteristics, and system design. Proper dilution and controlled addition are essential for maximizing performance.
8. Environmental and Operational Impact
Hydroxamated polyacrylamide contributes to greener and more efficient aluminum refining:
-
Reduces chemical and water consumption
-
Decreases volume of waste sludge
-
Improves recovery of reusable caustic soda
-
Minimizes risk of mud overflow or loss of containment
As environmental standards tighten and the cost of caustic soda and disposal rises, these benefits become increasingly valuable to refinery operators.
Conclusion
Hydroxamated (hydroxamic acid) polyacrylamide is a specialized flocculant used in alumina production facilities for efficient red mud settling, caustic soda recovery, and overflow liquor clarification. Its strong interaction with metal oxides, coupled with its high molecular weight and floc strength, makes it particularly well-suited for the harsh chemical and thermal conditions of the Bayer process. By incorporating hydroxamated PAM into key separation stages, aluminum plants can enhance productivity, reduce operating costs, and meet environmental performance goals—ensuring a more sustainable and efficient refining operation.