Our Products
Product Center / Hydroxamated(hydroxamic acid) flocculants used for aluminum red mud setting
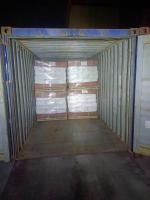
Application of Hydroxamated (Hydroxamic Acid) Flocculants in Aluminum Plants
Hydroxamated flocculants, based on hydroxamic acid functional groups, are a specialized class of high-performance polymers used in the mining and hydrometallurgical industries, particularly in aluminum refining plants. Their unique chemistry makes them particularly effective in flocculating fine particles and improving solid-liquid separation in Bayer process operations, which are central to aluminum production from bauxite ore. These flocculants offer targeted selectivity, high affinity for metal ions, and improved process efficiency.
1. Overview of the Bayer Process in Aluminum Plants
The Bayer process is the principal method for refining bauxite to produce alumina (Al₂O₃), which is later smelted to aluminum metal. The process involves several stages:
-
Digestion: Bauxite ore is treated with hot caustic soda (NaOH) to dissolve aluminum-containing minerals into sodium aluminate.
-
Clarification: The slurry is separated into red mud (residue) and clear sodium aluminate solution.
-
Precipitation: Alumina hydrate is precipitated from the solution.
-
Calcination: The hydrate is heated to produce alumina.
One of the most challenging steps is separating the red mud from the pregnant liquor (sodium aluminate solution) during clarification. This step requires highly effective flocculants, and hydroxamated polymers have proven to be particularly suitable for this role.
2. Role of Hydroxamated Flocculants in Red Mud Settling
Hydroxamated flocculants are primarily used to enhance the settling and clarification of red mud—the iron-rich residue produced during digestion. These flocculants significantly improve the rate at which red mud particles aggregate and settle out of suspension, allowing for faster recovery of clear liquor.
Advantages:
-
Selective adsorption on iron oxides and clays (key red mud components)
-
Efficient bridging between fine particles
-
Enhanced particle agglomeration
-
High floc strength and shear resistance
3. Mechanism of Action
Hydroxamic acid groups in the flocculant backbone have a strong affinity for metal oxide surfaces, especially iron (Fe³⁺) and aluminum (Al³⁺) oxides present in red mud. This chelation ability allows hydroxamated flocculants to anchor firmly onto red mud particles.
Once adsorbed, the polymer chains extend and bind to other particles, forming bridges that result in large, stable flocs. These flocs then settle rapidly under gravity, leading to faster clarification of the aluminate solution.
4. Application Points in Aluminum Refineries
Hydroxamated flocculants can be introduced at various points in the Bayer process, including:
a. Primary Settler (Thickener Feedwell)
-
The most common application point.
-
Flocculant is dosed into the feedwell of the red mud thickener to initiate floc formation.
-
Enhances mud settling rate and improves overflow clarity.
b. Secondary Thickeners
-
May be used to improve underflow density and minimize overflow solids.
c. Washer Circuits
-
Helps reduce mud carryover and loss of caustic soda in counter-current washing (CCW) circuits.
5. Benefits of Using Hydroxamated Flocculants
a. Improved Settling Rates
-
Dramatically increases the rate at which red mud settles, allowing thickeners to process higher throughput volumes or operate at higher mud loads.
b. Clearer Overflow Liquor
-
Results in lower turbidity and solids content in the pregnant liquor, improving the quality of downstream precipitation and filtration.
c. Higher Underflow Density
-
Produces denser mud that is easier to handle, transport, and dispose of, reducing water content and associated costs.
d. Reduced Caustic Loss
-
More efficient separation of red mud reduces the loss of valuable sodium hydroxide entrained in the residue.
e. Enhanced Floc Stability
-
Flocs formed are more resistant to shear forces, especially in high-throughput circuits or under intense mixing conditions.
f. Compatibility with Harsh Conditions
-
Performs effectively at high pH (13–14) and elevated temperatures (80–100°C) typical of Bayer process liquors.
6. Formulation and Handling
Hydroxamated flocculants are typically supplied as:
-
Liquid emulsions for ease of dosing
-
Powdered polymers (requiring solution preparation before use)
They are used at low concentrations (ppm level), but the exact dosage depends on:
-
Bauxite quality and composition
-
Particle size distribution in red mud
-
Processing temperature and pH
-
Thickener design and residence time
7. Environmental and Operational Considerations
a. Reduced Environmental Impact
-
By improving red mud compaction and reducing residual caustic soda, hydroxamated flocculants help minimize environmental risks associated with mud disposal.
b. Operational Efficiency
-
Increased throughput and improved liquor clarity lead to reduced downtime, better resource utilization, and lower operational costs.
8. Comparison with Conventional Flocculants
While traditional anionic polyacrylamide flocculants are also used in alumina refining, hydroxamated flocculants offer several distinct advantages:
Parameter | Anionic PAM | Hydroxamated Flocculant |
---|---|---|
Affinity to metal oxides | Moderate | High (strong chelation) |
Settling performance | Good | Excellent |
Floc strength | Moderate | High |
Clarity of overflow | Good | Superior |
Compatibility (pH, temperature) | Limited | High |
Dosage efficiency | Higher required | Lower dosage, higher effect |
9. Examples of Commercial Products
Some hydroxamated flocculants used in the aluminum industry include:
-
CYFLOC HX series (Cytec/Solvay)
-
Alclar HX series (SNF)
-
HYDROXAMATE-based custom polymers from regional suppliers
These are often customized to match site-specific bauxite characteristics and process parameters.