Our Products
Polyacrylamide / anionic polyacrylamide(zetag 4145)can be replaced by Chinafloc A series
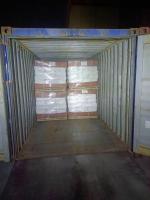
anionic polyacrylamide(zetag 4145)can be replaced by Chinafloc A series
zetag 4145 is a kind of anionic polyacrylamide with 50% hydrolysis degree and very high molecular weight.mainly used for water treatment and mineral processing.Chinafloc A5018 can replace of it with good performance.
Anionic polyacrylamide (APAM) is a versatile polymer widely used in various industries due to its exceptional flocculating and coagulating properties. These properties make it particularly effective in water treatment, mineral processing, and oilfield operations. Each of these applications leverages the unique chemical characteristics of anionic polyacrylamide to enhance process efficiency, improve environmental outcomes, and reduce operational costs. This essay explores the main functions of anionic polyacrylamide in water treatment, mineral processing, and oilfield operations, detailing how it contributes to the effectiveness of each application.
Anionic Polyacrylamide in Water Treatment
Water treatment is one of the most common and critical applications of anionic polyacrylamide. The primary function of anionic polyacrylamide in water treatment is to act as a flocculant, a substance that promotes the aggregation of suspended particles into larger clusters, or flocs, which can then be more easily removed from the water through sedimentation, filtration, or flotation. This process is essential in both municipal and industrial wastewater treatment to ensure that water is clean and safe for discharge or reuse.
1. Flocculation of Suspended Solids
In wastewater treatment, the main challenge is to remove suspended solids that are often too fine to be removed by simple filtration. Anionic polyacrylamide is highly effective at flocculating these particles because of its high molecular weight and anionic (negatively charged) nature. When added to wastewater, anionic polyacrylamide molecules adsorb onto the surfaces of suspended particles, neutralizing their charges and allowing them to come together to form flocs.
These larger flocs are much easier to remove through sedimentation or filtration processes, significantly improving the clarity of the treated water. The efficiency of flocculation directly impacts the overall effectiveness of the water treatment process, making anionic polyacrylamide a crucial component in achieving regulatory standards for water quality.
2. Reduction of Chemical Oxygen Demand (COD) and Biological Oxygen Demand (BOD)
In addition to flocculating suspended solids, anionic polyacrylamide can also help reduce the Chemical Oxygen Demand (COD) and Biological Oxygen Demand (BOD) of wastewater. COD and BOD are measures of the amount of organic pollutants in the water, which, if not adequately treated, can deplete oxygen levels in receiving water bodies, harming aquatic life.
By aggregating and removing organic matter along with suspended solids, anionic polyacrylamide reduces the load of pollutants in the wastewater, thereby lowering COD and BOD levels. This is particularly important in industries such as food processing, textiles, and chemicals, where high levels of organic pollutants are typically present in the effluent.
3. Sludge Dewatering
Another critical application of anionic polyacrylamide in water treatment is in sludge dewatering. The treatment of wastewater generates sludge, a byproduct that contains a mixture of water, organic matter, and inorganic solids. Efficiently dewatering this sludge is essential to reduce its volume and make it easier to handle and dispose of.
Anionic polyacrylamide is used to enhance the dewatering process by promoting the aggregation of fine sludge particles, allowing water to be more easily separated and removed. This results in a drier, more manageable sludge with reduced disposal costs and environmental impact.
Anionic Polyacrylamide in Mineral Processing
Mineral processing involves the extraction and processing of minerals from ores, which often includes separating valuable minerals from waste material. Anionic polyacrylamide plays a crucial role in this industry by improving the efficiency of various processes, including solid-liquid separation, tailings management, and mineral recovery.
1. Solid-Liquid Separation
In mineral processing, one of the primary functions of anionic polyacrylamide is to facilitate solid-liquid separation, a process essential for concentrating valuable minerals and removing waste materials. After minerals are extracted from the ore, the slurry—a mixture of water and finely ground ore—contains both valuable minerals and unwanted waste particles.
Anionic polyacrylamide is added to the slurry to induce flocculation of the fine particles, allowing them to settle more quickly. This process, known as sedimentation or thickening, separates the solid particles from the liquid, enabling the clear liquid to be decanted or filtered off. The more efficient the solid-liquid separation, the higher the concentration of valuable minerals, which improves the overall recovery rate and reduces processing costs.
2. Tailings Management
Tailings are the waste materials left after the valuable minerals have been extracted from the ore. These tailings are typically stored in large ponds, where they need to be managed to prevent environmental contamination. Anionic polyacrylamide is used in tailings management to promote the settlement of fine particles and reduce the volume of water in the tailings, making them more stable and easier to store.
By flocculating the fine particles in the tailings, anionic polyacrylamide enhances the dewatering process, reducing the risk of tailings pond overflows and minimizing the environmental impact of mining operations. Additionally, the improved settling of tailings reduces the need for large storage facilities, lowering the overall footprint of the mining operation.
3. Enhanced Mineral Recovery
In mineral processing, the goal is to maximize the recovery of valuable minerals while minimizing the loss of these minerals to waste streams. Anionic polyacrylamide can be used in various stages of the mineral processing circuit to enhance the recovery of valuable minerals.
For example, in flotation processes, where minerals are separated based on their hydrophobic properties, anionic polyacrylamide can be used to improve the aggregation of mineral particles, making them easier to recover. This increases the efficiency of the flotation process, resulting in higher yields of valuable minerals.
Anionic Polyacrylamide in Oilfield Operations
The oil and gas industry uses anionic polyacrylamide in several key processes, including drilling, enhanced oil recovery, and produced water treatment. The polymer’s ability to control fluid properties and promote solid-liquid separation makes it an invaluable tool in these operations.
1. Drilling Fluid Additive
In drilling operations, the stability of the borehole and the control of fluid loss are critical to successful drilling. Anionic polyacrylamide is commonly used as an additive in drilling fluids (also known as drilling muds) to improve their rheological properties.
The addition of anionic polyacrylamide to drilling fluids increases their viscosity, which helps to suspend and transport drill cuttings to the surface. This prevents the accumulation of cuttings in the borehole, which can lead to blockages and reduce the efficiency of the drilling process. Additionally, the polymer’s ability to control fluid loss by forming a thin, impermeable filter cake on the borehole walls helps to prevent the infiltration of drilling fluids into surrounding formations, maintaining borehole stability and reducing the risk of blowouts.
2. Enhanced Oil Recovery (EOR)
Enhanced Oil Recovery (EOR) techniques are employed to increase the amount of oil that can be extracted from a reservoir after primary and secondary recovery methods have been exhausted. Anionic polyacrylamide is used in EOR to improve the efficiency of water flooding, a common EOR technique.
In water flooding, water is injected into the oil reservoir to displace the remaining oil and push it towards production wells. Anionic polyacrylamide is added to the injection water to increase its viscosity, making it more effective at displacing the oil. The polymer’s long chain molecules increase the sweep efficiency of the water flood, reducing the amount of oil that is bypassed and left behind in the reservoir. This leads to higher oil recovery rates and extends the productive life of the oil field.
3. Produced Water Treatment
Produced water is the water that comes to the surface along with oil and gas during production. This water often contains a mixture of hydrocarbons, salts, and other contaminants that need to be treated before the water can be discharged or reused.
Anionic polyacrylamide is used in the treatment of produced water to promote the flocculation of suspended solids and hydrocarbons, allowing them to be more easily separated from the water. By aggregating these contaminants into larger particles, anionic polyacrylamide enhances the efficiency of separation processes such as sedimentation, flotation, and filtration. This results in cleaner produced water that meets environmental discharge standards or can be reused in other oilfield operations.
Conclusion
Anionic polyacrylamide is a critical component in water treatment, mineral processing, and oilfield operations, where its primary functions include flocculation, solid-liquid separation, and fluid control. In water treatment, anionic polyacrylamide enhances the removal of suspended solids, reduces COD and BOD levels, and improves sludge dewatering. In mineral processing, it facilitates solid-liquid separation, aids in tailings management, and enhances mineral recovery. In oilfield operations, anionic polyacrylamide improves drilling fluid performance, boosts enhanced oil recovery, and enhances produced water treatment.
The use of anionic polyacrylamide in these industries not only improves process efficiency and product quality but also contributes to environmental protection by reducing waste and minimizing the impact of industrial activities. As these industries continue to evolve, the role of anionic polyacrylamide will remain essential in ensuring sustainable and efficient operations.