Our Products
Polyacrylamide / The equivalent of cyfloc HX-6200 used for settling mud in red mud clarifiers or CCD mud washing circuits.
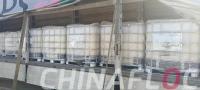
The equivalent of cyfloc HX-6200 used for settling mud in red mud clarifiers or CCD mud washing circuits.
Introduction
In mineral processing and metallurgical plants, the treatment and management of fine particulate matter is a critical aspect of plant operation. For lumina plants that process bauxite or other ores, red mud is a common byproduct that contains extremely fine particles which, if left untreated, can cause significant operational challenges. Anionic flocculant emulsions are widely employed to facilitate the rapid and efficient settling of these fine particles in clarifiers and to enhance the dewatering performance in CCD mud washing circuits.
Red Mud and Its Challenges
Red mud is a waste residue generated during the Bayer process, a method used to refine bauxite into alumina. The residue is characterized by:
- High alkalinity: The red mud is typically caustic, with high pH values.
- Fine particle size: The particles are extremely fine and colloidal in nature, making them difficult to settle by gravity alone.
- High water content: Due to the very fine size and high viscosity, red mud retains a significant amount of water, which presents challenges in storage, disposal, and environmental management.
Due to these factors, red mud often requires additional processing steps, including flocculation and sedimentation, to reduce its volume and improve handling. In particular, clarifiers and CCD circuits are designed to separate solids from the process water and to enhance the efficiency of subsequent dewatering processes.
Role of Anionic Flocculant Emulsions
Flocculation is a process where small, dispersed particles aggregate into larger particles (flocs) that settle more quickly under gravity. Anionic flocculant emulsions are specifically designed for systems with particular chemical conditions. In the case of red mud clarifiers and CCD circuits, the choice of an anionic flocculant is significant for several reasons:
-
Charge Compatibility:
Red mud particles typically have a positively charged surface due to the alkaline conditions and the composition of the particles. Anionic flocculants, which carry a net negative charge, are highly effective in neutralizing these positive charges. This charge neutralization reduces the electrostatic repulsion between particles, allowing them to come together to form larger aggregates. -
Emulsion Stability and Dispersion:
The emulsion form of the flocculant enhances its distribution within the process water. Emulsions are stable dispersions of the polymer in a carrier fluid (often water or oil) and facilitate the rapid delivery and uniform mixing of the flocculant throughout the red mud suspension. This ensures that the flocculant can interact effectively with the suspended particles. -
Optimized Dosage and Performance:
Anionic flocculant emulsions are designed to operate effectively at low dosages. This minimizes the overall chemical cost while providing significant improvements in settling performance. The optimized dosage helps in achieving a balance between floc formation and maintaining the permeability of the settled sludge, which is important for subsequent dewatering steps.
Application in Red Mud Clarifiers
Red mud clarifiers are sedimentation tanks that allow the flocculated particles to settle out of the process water. The application of anionic flocculant emulsions in these clarifiers involves several key operational aspects:
-
Preparation and Dosing:
The flocculant emulsion is typically stored in a dedicated dosing system and is carefully metered into the clarifier’s influent stream. The dosing system is calibrated to deliver the required dosage based on the flow rate, particle concentration, and process conditions. The goal is to achieve optimum floc formation without over-dosing, which could lead to the formation of excessively large or fragile flocs. -
Mixing and Floc Formation:
Upon dosing, the flocculant is rapidly mixed with the red mud suspension. High-intensity mixing ensures that the flocculant comes into intimate contact with the fine particles. As the anionic polymer adsorbs onto the positively charged surfaces of the particles, bridging between particles occurs, leading to the formation of larger flocs. The size and density of these flocs are critical factors that determine the settling velocity and the clarity of the overflow water. -
Settling and Clarification:
With enhanced flocculation, the larger and denser aggregates settle more quickly in the clarifier. This rapid settling is vital for maintaining a high throughput in the plant and ensuring that the process water, which is often recycled or discharged, meets the required clarity and quality standards. Effective settling also minimizes the carryover of solids into subsequent processing steps, reducing the risk of process upsets or equipment wear.
Application in CCD Mud Washing Circuits
Counter Current Decantation (CCD) is a multi-stage process used to wash and dewater sludges, such as red mud, by counter-flowing clean water through the sludge bed. Anionic flocculant emulsions are used in CCD circuits for several reasons:
-
Improved Solid-Liquid Separation:
In CCD circuits, the addition of anionic flocculant helps in aggregating the fine particles, resulting in improved separation between the solids and the process water. This improved separation is critical in achieving a higher degree of dewatering and reducing the moisture content of the sludge. -
Enhanced Washing Efficiency:
By forming stronger and more resilient flocs, the washing process becomes more effective. The flocs retain their structure during the counter current flow, allowing the clean water to wash out residual impurities and entrained chemicals more effectively. This is particularly important in reducing contaminants that could interfere with downstream processes or environmental discharge standards. -
Increased Process Throughput:
The enhanced flocculation and settling performance provided by the anionic flocculant emulsion can lead to an increase in the overall throughput of the CCD circuit. With faster settling and more efficient washing, the circuit can operate at a higher capacity, reducing the overall residence time and improving the economic efficiency of the plant. -
Optimizing Dewatering and Sludge Handling:
The final goal in CCD circuits is to achieve a sludge with lower water content that can be more easily handled, transported, or further processed. Anionic flocculant emulsions contribute to achieving this by producing a more permeable sludge structure, which facilitates water removal during subsequent dewatering steps such as filtration or centrifugation.
Practical Considerations and Optimization
When applying anionic flocculant emulsions in lumina plants, several practical considerations must be addressed:
-
Process Monitoring:
Continuous monitoring of parameters such as pH, temperature, turbidity, and floc size is essential to ensure optimal performance. Adjustments in the flocculant dosage may be required based on variations in the red mud composition and process conditions. -
Compatibility with Other Chemicals:
In many processing plants, multiple chemicals are used concurrently. It is important to ensure that the anionic flocculant does not adversely interact with other reagents or process additives. Laboratory and pilot-scale tests are often conducted to verify compatibility and to fine-tune dosing protocols. -
Economic Considerations:
The cost-effectiveness of using anionic flocculant emulsions is a key consideration. The benefits of improved settling and dewatering must be weighed against the cost of the flocculant, with optimization studies conducted to minimize chemical usage while maximizing performance. -
Environmental Impact:
The choice and use of flocculants can have environmental implications. Modern formulations are designed to be as benign as possible, but proper handling, storage, and disposal of flocculant-containing waste streams are critical to minimizing environmental impact.
Conclusion
In summary, anionic flocculant emulsions play a pivotal role in the effective treatment of red mud in lumina plants. By neutralizing the positive charges on red mud particles and facilitating the formation of larger, denser flocs, these flocculants improve the settling performance in red mud clarifiers and enhance the efficiency of CCD mud washing circuits. This results in clearer process water, improved sludge dewatering, and a more efficient overall process, contributing to operational efficiency and cost-effectiveness. The successful application of these flocculants relies on careful optimization, monitoring, and integration into the plant’s broader process control strategies.