Our Products
Polyacrylamide / Anionic polyacrylamide magnafloc 5250 equivalent model of Chinafloc A2520
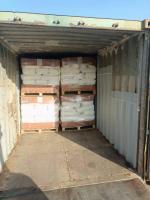
Anionic polyacrylamide magnafloc 5250 equivalent model of Chinafloc A2520
Main Application of Magnafloc 5250
Magnafloc 5250 is a high molecular weight, anionic polyacrylamide-based flocculant widely used in various industrial and environmental applications. Its primary and most significant application lies in the solid-liquid separation processes commonly found in mineral processing and mining operations. Within these contexts, Magnafloc 5250 is deployed to improve the efficiency of separation stages, enhance the clarity of process water, accelerate sedimentation rates, and facilitate the thickening and filtration of mineral slurries. As such, this product is a critical element in achieving higher productivity, better resource recovery, and improved environmental compliance in large-scale mineral extraction and refining activities.
Contextual Overview
In the mining and mineral processing industry, handling large volumes of finely ground solids suspended in water is commonplace. Ore beneficiation, concentration, and separation processes produce significant amounts of tailings and process water that require treatment before recirculation or disposal. Traditional gravity settling and mechanical separation methods can be slow, inefficient, or incomplete, leading to poor process outcomes, excessive water consumption, and potentially serious environmental issues.
Flocculants, like Magnafloc 5250, have emerged as powerful tools for addressing these challenges. By bridging or binding together individual particles, they create larger aggregates (flocs) that settle or separate from the water more easily. This action reduces the overall turbidity and solids content of process water, producing a cleaner overflow suitable for reuse. Simultaneously, it consolidates solids into a denser, more manageable underflow, aiding in the efficient handling and disposal of tailings or their further processing.
Chemical and Physical Characteristics
Magnafloc 5250 belongs to a class of synthetic, water-soluble polymers derived from acrylamide. The polymer chains are typically very long, with high molecular weight, and are often modified with various anionic functional groups. These anionic charges enable the flocculant to interact strongly with suspended solids, especially minerals or fine particles that carry surface charges. The polymer’s large molecular structure extends into the water, capturing particles through bridging mechanisms—imagine long, chain-like molecules latching onto multiple particles simultaneously, effectively gluing them together into bigger clumps.
This “bridging” mechanism is central to Magnafloc 5250’s function. By increasing the size and mass of particle aggregates, the product drastically improves sedimentation rates within thickeners, clarifiers, and settling tanks. Consequently, the treated slurry rapidly separates into a clarified, low-turbidity supernatant (overflow) and a concentrated, settled underflow.
Primary Application in Mineral Processing
In mineral processing plants—such as those handling copper, iron, gold, phosphate, or coal—fine particles generated during grinding and milling must be efficiently separated from water. Poorly clarified process water can reduce the efficiency of downstream processes and increase the load on filtration equipment. Tailings, when not effectively thickened, may require more extensive storage facilities and could present environmental risks if not managed properly.
-
Thickening of Tailings: One of the main applications of Magnafloc 5250 is in tailings thickening operations. After the valuable minerals are extracted and concentrated, the remaining slurry (tailings) contains finely dispersed solids that must be stored or disposed of responsibly. Using this flocculant in a thickener helps produce a denser underflow, meaning that the resulting tailings have a higher solids concentration and, consequently, reduced volume. This makes them easier to handle, store, and transport—improving the economics of the disposal process and reducing the footprint of tailings dams.
-
Clarification of Process Water: Many mineral processing circuits rely on reused water. The water recovered from thickeners, after treatment with Magnafloc 5250, is generally much clearer and lower in suspended solids. This clarified water can be recycled back into the process, reducing the need for fresh water intake. This recycling practice conserves scarce resources and minimizes the environmental impact of the mining operation. Cleaner process water also means fewer operational issues: pumps run more efficiently, pipelines clog less frequently, and downstream treatment processes (such as flotation or filtering) benefit from more consistent feed quality.
-
Improved Filtration and Dewatering: In addition to sedimentation-based processes, Magnafloc 5250 can enhance the efficiency of filtration and other mechanical dewatering stages. By producing larger and more robust flocs, the product simplifies the task of removing water from the solids. Filters (e.g., vacuum filters, pressure filters, or belt filters) can operate more effectively, producing dryer cakes and reducing energy consumption in subsequent drying steps.
Broader Industrial and Environmental Applications
While its main application is indeed in mineral processing, Magnafloc 5250 also finds use in other industries that require solid-liquid separation. It can be employed in:
-
Industrial Wastewater Treatment: Facilities that generate wastewater with suspended solids—such as chemical plants, pulp and paper mills, or food processing factories—can use Magnafloc 5250 to improve the removal of particulates, reduce turbidity, and meet regulatory discharge limits.
-
Municipal Wastewater Treatment: Although not always the primary flocculant of choice in municipal settings (where aluminum or iron-based coagulants often dominate), Magnafloc 5250 can still serve as a valuable aid in clarifying secondary effluent or thickening biosolids prior to sludge dewatering.
-
Other Mining Processes: Beyond tailings thickening, some specialized mineral concentration or refining processes may benefit from the improved clarity and filtration rates afforded by this polymer.
Despite these additional applications, it remains that the mining and mineral processing sectors represent the core market for Magnafloc 5250, where the economic and operational benefits are most pronounced.
Key Advantages in Practical Use
-
Enhanced Process Efficiency: By providing better floc formation and faster settling rates, Magnafloc 5250 shortens settling times in thickeners and clarifiers, increasing throughput and reducing bottlenecks. Plants can handle larger volumes without incurring additional capital costs for bigger equipment.
-
Water Conservation: Because the overflow from thickeners and clarifiers is cleaner, it can be recycled with fewer complications. This approach helps operations minimize their environmental impact by reducing fresh water usage and lowering the risk of environmental contamination.
-
Reduced Environmental Footprint: The improved thickening of tailings leads to a more compact residue, easing the strain on tailings storage facilities. Denser tailings can be deposited in smaller areas, reducing the total land required for waste disposal. This spatial efficiency not only cuts down on operational costs but also eases the long-term environmental burden.
-
Cost Savings: While polymers like Magnafloc 5250 represent an additional chemical cost, the resulting operational savings—less downtime, improved equipment performance, more efficient water use, and smaller environmental management expenses—often offset these expenditures. The return on investment is realized through smoother operations, optimized material handling, and compliance with regulatory standards that might otherwise incur fines or mandates for expensive remediation.
-
Flexibility and Adaptability: Magnafloc 5250 can be fine-tuned to work under a variety of conditions. Operators can adjust concentration, dosage, and application points to suit the nature of the slurry, the mineral type, pH conditions, temperature, and solids concentration. This flexibility ensures the product’s effectiveness in a broad range of scenarios.
Operational Considerations and Best Practices
To maximize the benefits of Magnafloc 5250, proper handling and usage guidelines should be followed:
-
Dosage Optimization: Overdosing or underdosing reduces efficiency. Laboratory tests and onsite pilot trials help determine the optimal polymer concentration, ensuring the best possible performance at the lowest practical cost.
-
Proper Mixing and Addition Points: The flocculant should be thoroughly mixed into the slurry to ensure even particle coverage. Strategic addition points along the process flow can enhance floc formation and minimize polymer waste.
-
Compatibility with Other Chemicals: In complex mineral processing circuits, multiple reagents (e.g., coagulants, pH adjusters, flotation reagents) may be used. Ensuring compatibility among these chemicals is crucial. Magnafloc 5250 generally works well with various process chemistries, but testing is advisable.
-
Staff Training: Operators and technicians should be properly trained in the handling, storage, and preparation of the flocculant solution. Safety measures and equipment maintenance protocols must be established to guarantee continuous, trouble-free operation.