Our Products
Oilfield Chemicals / DRA|Drag reducing agent|flow improver|drag reducer
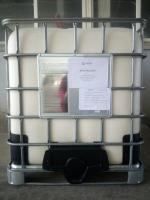
DRA|Drag reducing agent|flow improver|drag reducer
1.specifications:
Properties |
Test result |
Test Method |
Apperance |
White slurry |
---- ---- |
Solid contecnt(%) |
30.1% wt |
GB/T 1725-2007 |
Viscosity 25℃ |
270mPa.s 100S-1 |
Rotationl Viscometer |
Drag Reduction(20ppm) |
61.4%(Re=14000) |
SY/T 6578-2009 |
Density(20℃-25℃) |
0.869g/ml |
GB/T6750 |
The maximum particle size of polymer |
<300um |
Laser particle analyzer |
Oil soluble test |
Qualified |
Q/LKS 01-2014 |
2.how to works:
Drag reducers, also known as drag reducing agents (DRA) and flow improvers, are any material that reduces frictional pressure loss during fluid flow in a conduit or pipeline. Pressure loss reduction is achieved by reducing the level of turbulent motion in the flow. Using DRA allows increased flow using the same amount of energy or decreased pressure drop for the same flow rate of fluid in pipelines. The current class of DRA, consisting of long-chain hydrocarbon polymers that act as turbulence inhibitors along the pipe wall to decrease the amount of energy lost in turbulent activity.
Frictional pressure drop, or drag, is a result of the resistance encountered by flowing fluid coming into contact with the pipe wall. There are generally two types of flow – laminar and turbulent. The friction pressures observed in laminar flow cannot be changed unless the physical properties of the fluid are changed. The current class of DRA does not change fluid properties and hence is effective only in turbulent flow. In most petroleum pipelines, the liquid flows through the pipeline in a turbulent
regime. Therefore, current DRA can perform very well in most pipelines.
In a turbulent flow regime, the fluid molecules move in a random manner, causing much of the energy applied to them to be wasted as eddy currents and other indiscriminate motion. DRA works by an interaction of the polymer molecules with the turbulence of the flowing fluid.
3.What is the true value of using DRA(drag reducing agent)?
DRA is a fascinating solution from a technical perspective, but the ultimate question, especially in today’s economy, is how does this make or save our company money? From my experience there are three ways DRA can be justified as a value add solution.
1) Throughput:
Firms that supply drag-reducing polymers state that flow increases in the range of 5-60% can be realized. This depends on system specifics such as available pumping capacity (is there available curve on the existing pumps to increase flow rate?), batching operations, booster stations, and lateral receipt configuration.
From my experience, a simple system with one commodity can definitely achieve a continuous 40% increase to flow. I have also achieved continuous flow increases of up to 30% on more complex systems with crude and condensate batching operation.
Increasing flow results in additional monthly throughput and thus increased revenue for a pipeline. It can also be a bridging solution between current system capacity and your future pump station upgrade capacity. An economic analysis may also suggest that DRA is a substitute to a system mechanical upgrade.
2) Energy Savings:
Maximizing throughput is not always a need for midstream companies. Perhaps a midstream company owns a pipeline in an area that doesn’t expect to see new volumes contracted. In this situation, DRA can provide an opportunity for reducing operating costs through pumping energy consumption. Pumps consume energy (electricity, fuel, or gas) in order to pump hydrocarbons down pipelines. DRA has the ability to reduce the line pressure of the pipeline, resulting in the pumps requiring less energy to transport the same amount of product.
Once again you can complete a simple economic analysis to determine the cost/benefit of such a scenario. Keep in mind contract terms for pump energy supply, transport contracts, and DRA supply contracts.
3) Operational flexibility:
There are two main areas I consider when evaluating DRA as a solution for operational flexibility. The first is along the lines of the Redbull effect; yes I am talking about the energy drink. There are occasions when pipelines would like to have the opportunity to turbo charge their flow rates for a finite period of time. An example would be when starting up a pipeline after a lengthy outage where facility tanks have become full of product. DRA can provide an economic solution to empty storage quickly and make up the lost pumping time with the goal of maintaining the pipeline’s typical capacity. This is a great solution as upstream customers will be less likely to experience a take-away reduction due to the outage.
The second area of operational flexibility is regarding pressure restrictions of pipelines, typically due to integrity events. There are times midstream companies choose to reduce the MOP (maximum operating pressure) of a pipeline as a precautionary effort during mitigation activities. Pressure restrictions on a pipeline may result in decreased flow rates if the pipeline was running at design capacity. Injecting DRA would result in a reduction of pipeline pressure, allowing an increase of flow rate to pre-pressure restriction levels.
tag:anionic polyacrylamide manufacturers,anionic polyacrylamide ,anionic flocculant ,APAM,drag reducing agent
tag:
DRA,Drag reducing agent,flow improver,drag reducer